The Sustainable Swimwear Fabrics to Know: ECONYL, REPREVE, and Amni Soul Eco® Thread
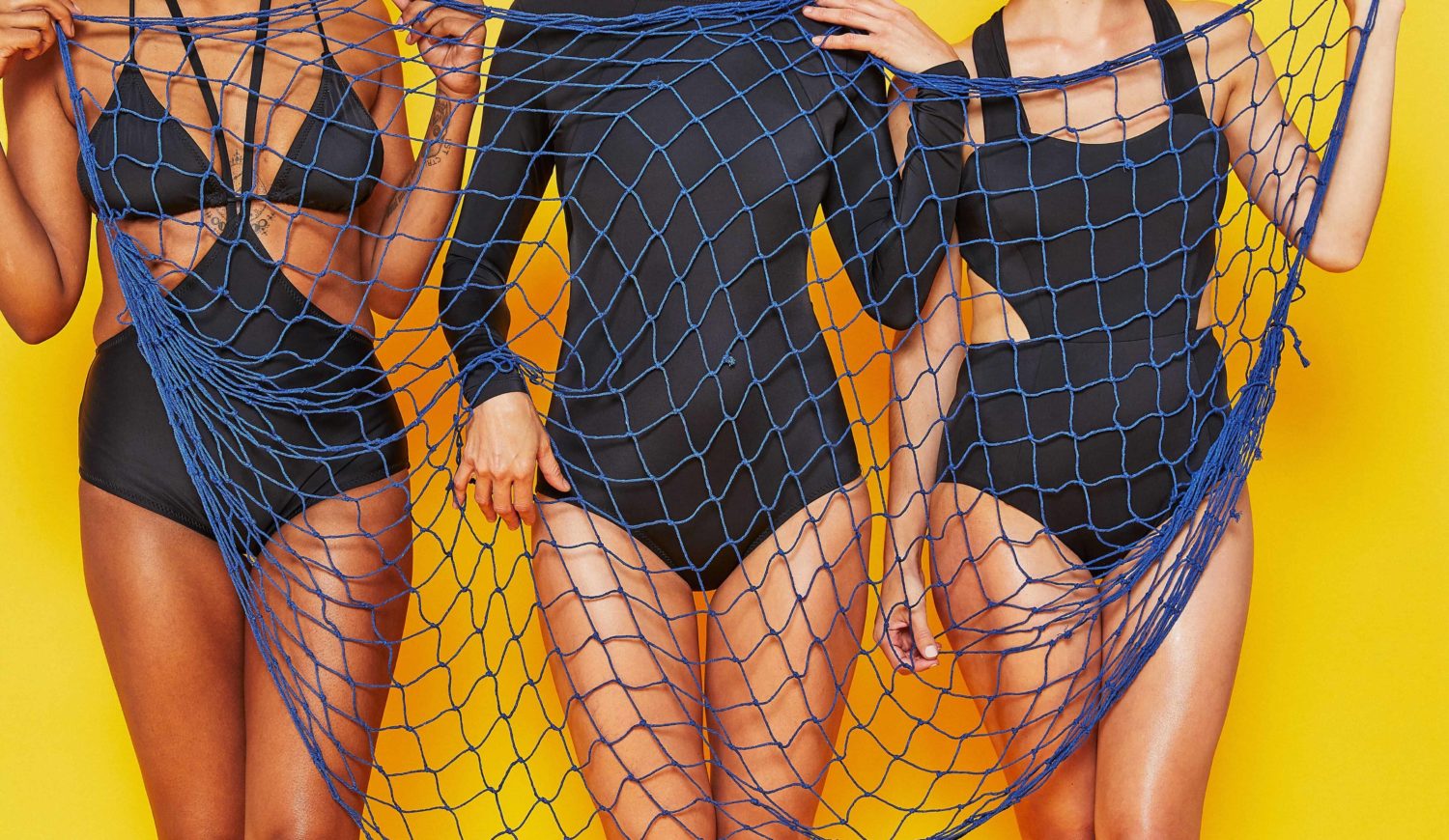
TL;DR ECONYL is made from regenerated nylon and Repreve is made from recycled plastic bottles. Amni Soul Eco® Thread is the world's first recyclable and biodegradable polyamide yarn. This post dives into exactly how each of these fibers is made and three brands using these fibers: Saturday Swimwear, Sensi Graves, and BOLD Swim.
The vast majority of swimsuits on the market are made from synthetic fabrics — and it’s not hard to see why. Synthetic fabrics have performance qualities that enable swimsuits to have the necessary stretch and durability as well as resistance to chlorine, saltwater, and sunlight.
However, synthetic fabrics come at a cost to the environment, requiring massive amounts of energy and petroleum for their production all while creating non-biodegradable waste in the process.
Fortunately, with the advancement of recycled and regenerated materials, wearing high-performance swimwear can still be sustainable. New innovative synthetic fabrics are creating new life out of materials that would’ve otherwise gone to waste, and are reducing the demand for petroleum.
Synthetic fabrics, however — recycled or not — shed microfibers when washed. These microfibers pollute our oceans and waterways endangering wildlife and putting drinking water at risk. To prevent microfibers from being released in your washing machine, we recommend placing any clothing or swimwear made with synthetic fibers in a microfiber catching bag like the Guppyfriend Washing Bag.
About REPREVE
REPREVE is a performance fiber made from recycled plastic bottles. To guarantee the recycled content in their fabrics, REPREVE uses a tracing technology that verifies recycled content claims.
The company that makes REPREVE, Unifi, is a global textile solutions company that has recycled over 16 billion plastic bottles to date, with the goal to recycle 20 billion bottles by 2020.
Behind the Process of the Fiber
First, recycled post-consumer plastic bottles are collected, sorted, baled, cleaned, and chopped into flakes before being sent off to the REPREVE recycling center — one of the most advanced recycling facilities in the United States. At the facility, the bottle flakes are turned into REPREVE chips and put into massive silos — each silo holds the equivalent of 27 million recycled bottles. The REPREVE chips are blended, melted, and extruded to make REPREVE fiber. This unique fiber has inherent performance properties, such as moisture-wicking, thermal regulation, order control, cushioning, and resilience.
The fiber is then transformed into the fabric and cut and sewn into a wide variety of products — from clothing to car interiors!
About ECONYL
ECONYL is a type of regenerated nylon made from waste from landfills and oceans. Going beyond the conventional recycling process, ECONYL uses regeneration, which ensures that the new fabric is exactly the same as virgin raw nylon — meaning ECONYL has like-new qualities and can be infinitely recycled and recreated into new products.
To put the impact of ECONYL into numbers, for every 10,000 tons of ECONYL material made, it spares 57,100 tons of carbon dioxide being emitted into the atmosphere and 70,000 barrels of crude oil from being used.
Behind the Process of the Fiber
ECONYL is made using a closed-loop regeneration process. The first step is to rescue the waste from oceans and landfills from across the globe, including throughout the U.S., Canada, Greece, Egypt, Thailand, and Norway. ECONYL specifically looks for items with nylon in them, including used carpets, clothing, and discarded fishing nets.

The nylon that was in those items is then separated, cleaned, shredded, compacted, and packed in a waste treatment center in Slovenia. That nylon is then transported to ECONYL’s regeneration facility.
The next step, called ECONYL Depolymerization, is an innovative proprietary system where nylon’s six molecules are unzipped and returned to their monomer state. These monomers are then bonded together again to other identical monomers to form the nylon six polymer in ECONYL’s Polymerization process. Monomers are the simplest units of polymers, and the process of linking these monomers to form polymers is called polymerization.
After this advanced transformation process, the ECONYL is sent to production facilities where it’s processed into yarn for commercial use. The company produces carpet yarn for the home interiors industry and textile yarn for the fashion industry.
ECONYL is commonly used for carpeting and apparel, especially in swimwear and activewear. What’s incredible about the regeneration process is that once these ECONYL products have reached the end of their lifecycle, the fabric can enter back into the regeneration process and be transformed into like-new nylon once again.
About Amni Soul Eco® Thread
While most eco friendly synthetic fibers focus on reducing waste on the front-end by using recycled materials, Amni Soul Eco® Thread has taken an approach considering the end-of-life for its yarns, creating the world’s first recyclable and biodegradable polyamide yarn.
While the yarn is as resistant and durable as other polyamide yarns when worn, it will biodegrade within 5 years into organic matter (biomass) and biogas in a landfill environment.
Behind the Fiber
Amni Soul Eco® Thread has been specifically designed to biodegrade relatively quickly in anaerobic (i.e. oxygen-less) landfills by allowing bacteria to digest the waste materials in order to accelerate the biodegradation process.
About Recycled PET Fabric
Recycled polyethylene terephthalate fabric, also known as RPET, is made from breaking down post-consumer plastics such as discarded plastic water bottles. Making RPET fabric not only takes considerably fewer carbon emissions to produce than virgin PET, but it also helps redirect plastics that would otherwise go directly into landfills or the ocean. RPET is also nearly identical in quality compared to virgin polyester fabrics, so it lasts just as long and is better for the environment.
Behind the Process of the Fiber
The most common way RPET is created is when discarded plastics are washed, shredded, and re-spun using the same process that virgin polyester goes through to become textiles and apparel. But RPET can also be made through chemical recycling — a process where plastics are broken down into their fundamental components and rebuilt into fibers that are identical to virgin polyester.
Brands Using These Sustainable Fibers
Sensi Graves
Sensi Graves is a women-run and-owned brand with high-quality, sustainably made swimwear. Founder Sensi Graves is a professional kiteboarder and is dedicated to creating comfortable, performance-level suits to empower women in sports.
All of the brand’s swimwear is made in the U.S. by seamstresses who earn fair wages, and the pieces in our Sensi Graves collection are made from either ECONYL or REPREVE. The swim brand also donates 1% of every purchase to nonprofits committed to environmental protection.
Saturday Swimwear
Saturday Swimwear is a sustainable, women-owned brand with swimwear all handmade in the United States. Emily Laplume, the owner and designer behind the label, sews each and every piece herself in her van as she travels across the country. The brand’s earth-friendly, durable fabric is made from a blend of ECONYL and LYCRA XTRA LIFE.
Considering their impact across every step of the production process, Saturday Swimwear uses entirely biodegradable and compostable materials for their packaging.
BOLD Swim
BOLD Swim is an eco-minded size-inclusive swimwear brand (S – XXL) using Amni Soul Eco® Thread / CO2 Light Fabric for their sleek bikinis and one-pieces. The unique fabric BOLD swim uses has been designed with its end-of-life in mind from the beginning — Amni Soul Eco® Thread is nylon produced in Brazil that is completely biodegradable in landfills within 5 years!
This Black-owned business considers their sustainability practices beyond the fabric used, too, by using only non-toxic-dyes for their suits and upcycling any fabric waste from production into rugs and mats made by local artists in Brazil.